Green, low-carbon, and sustainable development to create a “lighthouse factory” in the motor industry
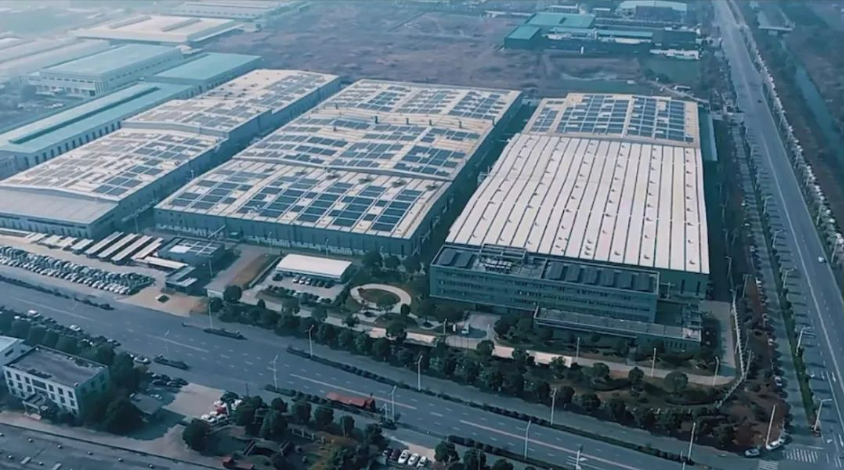
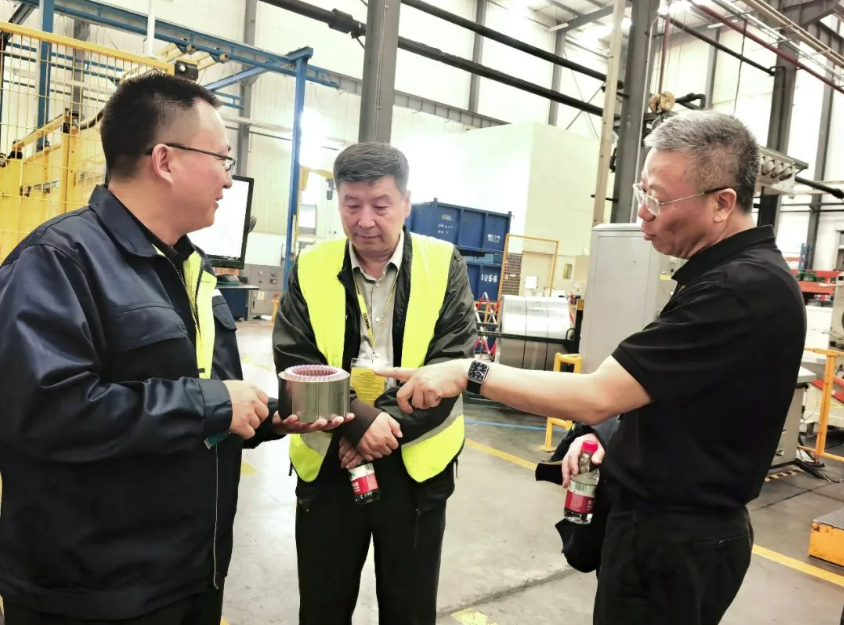
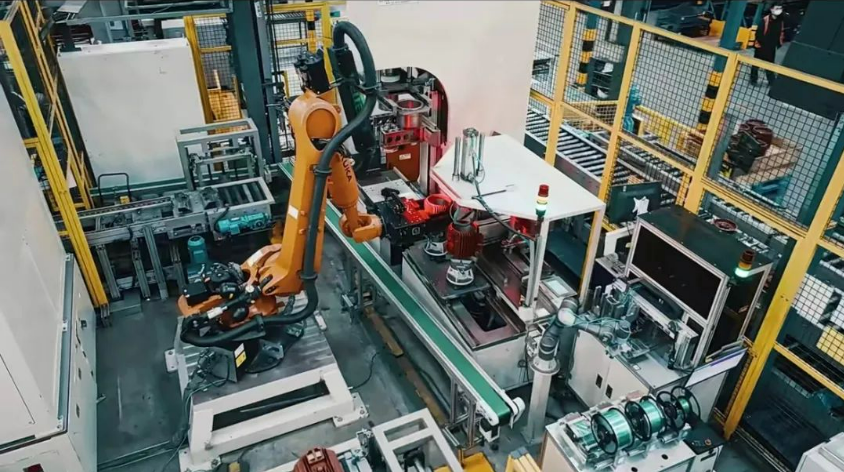
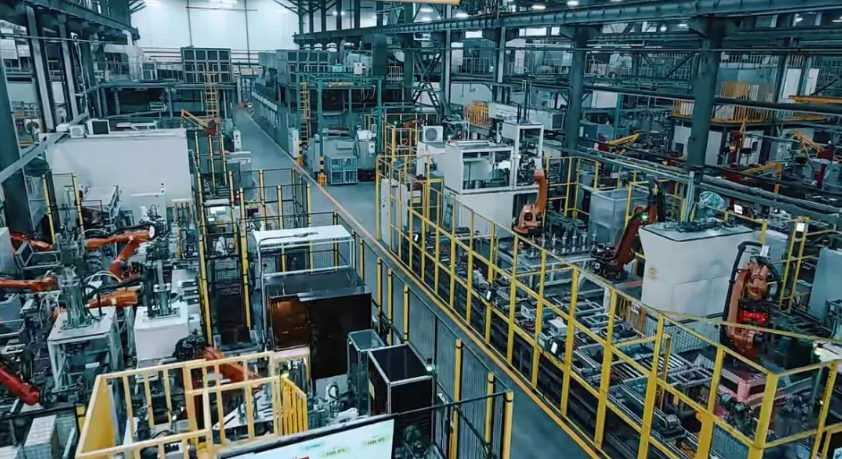
Email: sales5@xrjdcs.com
WhatsApp/Moblie: +86 18250705533
The industrial intelligent computer, which deeply integrates computer science and industrial automation technology, has recently made its debut in Shenzhen. This product integrates the calculation and control of industrial sites, greatly improving the performance of the calculation and control system.
Industrial intelligence machine series technology innovation originates from the Institute of Computing Technology, Chinese Academy of Sciences. “Industrial intelligence machine has achieved a breakthrough in key technologies in the field of high-end industrial control computing, laying a solid foundation for the development of intelligent manufacturing,” said Han Yinhe, a researcher at the Institute of Computing Technology of the Chinese Academy of Sciences.
The series of industrial intelligent machine products based on PC technology is a major achievement in promoting the transformation of scientific and technological achievements and upgrading traditional industries through the cooperation of “industry university research application investment”. It demonstrates the latest progress of Chinese enterprises in grasping the new trend of industrial automation development and promoting new quality production through technological innovation.
Industrial automation is the foundation and upstream of industry, and China has long been relatively weak in global competition in this field. To develop new industrialization, promote new quality productivity, and achieve independent and controllable industrial automation equipment is an inevitable path.
In recent years, the digital transformation of the manufacturing industry has deepened, and industrial sites have become increasingly complex. Previously, industrial control often involved relatively simple control algorithms and application software; Nowadays, industrial sites involve more process algorithms, AI algorithms, complex motion control algorithms for more axes, etc. Therefore, a more powerful computing terminal that can match the application is needed to complete them.
Compared with traditional industrial control systems, the new industrial intelligence machine integrates all functions of PLC (Programmable Logic Controller), industrial computer, motion controller, motion control card, industrial gateway, and edge server, pushing the traditional “customized hardware+closed software” mode towards a new mode of “unified hardware+intelligent software”. The biggest feature of this series of products is the integration of computing and control.
There are two major “souls” of artificial intelligence machines: one is the independently developed industrial operating system MetaOS; The second is the self-developed industrial programming platform MetaFacture. Li Xiaoning, Senior Product Director of Zhongke Era, said that the industrial intelligent machine product system can bring users three major values: first, simplifying the control system; Secondly, shorten the development cycle; The third is to improve the efficiency of remote operation and maintenance for users through deep integration of IoT technology.
At present, industrial intelligence machines and related technologies are being applied in industries such as semiconductors, lasers, 3C electronics, photovoltaics, wind power, petroleum, and steel, and industrialization is steadily advancing, becoming a strong support for promoting industrial intelligence.
Industrial grade touch display is an industrial display with touch function, and common touch methods include capacitive touch and resistive touch. It is a device used in industry and has significant differences from ordinary displays.
Industrial grade touch displays consist of three parts: LCD touch screen, functional motherboard, and housing. The structural material is generally made of aluminum alloy, which has good performance in heat dissipation, electromagnetic interference resistance, high and low temperature resistance, dust and water resistance, and earthquake resistance. Industrial grade touch displays have high environmental requirements. Industrial displays not only need to adapt to various industrial environments, but also maintain stable operation around the clock, which ordinary commercial displays cannot achieve.
Although the use of industrial grade touch displays is becoming increasingly widespread and can be seen in many daily life scenarios and industrial sites, many customers are still not very familiar with industrial grade touch displays. Below, the editor will provide a detailed introduction to the classification of industrial grade touch displays and their application knowledge.
1. Embedded industrial grade touch display: Embedded industrial grade touch display, as the name suggests, is a display embedded in the customer’s product equipment. The customer’s product or equipment must have a large or medium-sized control cabinet, with all components embedded in the client device except for the display panel, fixed with hooks on the back. The large control cabinet should be installed with holes according to the opening size in the embedded installation diagram of the industrial grade touch display manufacturer.
2. Wall mounted industrial grade touch display: The wall mounted industrial grade touch display can be hung, not only on the wall, but also installed on customer equipment. The angle of the industrial display can be adjusted according to customer requirements. Using appropriate mounting arms, industrial grade touch displays can be installed in any position for users to view, generally used for small, medium, and large devices.
3. Rack mounted industrial touch display: Generally speaking, rack mounted industrial touch displays are installed on cabinets, such as 21 inch cabinets, so their width is the standard 21 inches, the mounting holes are standard, and the dimensions are basically fixed. Rack mounted industrial grade touch displays are generally used in large cabinets, such as telecommunications, power supplies, and large servers.
4. Open industrial touch display: Industrial touch displays do not have a frame, only an internal display panel. Customers mainly use them on small-sized devices, and the installation space for industrial displays is generally not large, such as ATM machines, commercial POS machines, etc. They are usually installed in customer devices.
5. Embedded industrial grade touch display: Simply put, an embedded industrial grade touch display is an industrial display installed in the customer’s cabinet and equipment in reverse, inside the client device. Unlike open industrial grade touch displays, it is installed from the inside of the device, with its edges coinciding with the edges of the customer’s device casing. Embedded industrial grade touch displays are commonly used in large and medium-sized equipment such as the power, machinery, and medical industries.
Aluminum, lightweight and tough, is an indispensable basic raw material in modern industry. Due to its light texture and excellent chemical corrosion resistance, aluminum can occupy a “place” in many industrial fields, from aerospace to transportation equipment, from construction and packaging materials to chemical equipment. While playing a crucial role, the production of electrolytic aluminum also faces problems such as high energy consumption, low level of refined management in production and operation, and urgent need to improve the professional skills of talents.
Production safety cannot be ignored. Therefore, building a digitalized and intelligent production management model through digital and intelligent technologies has become a trend to promote the green and low-carbon development of the industry.
In this context, Inspur Cloud has developed the “Knowledge Industry Model” for the industrial sector. With advantages such as industrial data analysis, industrial knowledge reasoning, and industrial code generation, the digital empowerment of the aluminum industry has enabled it to move towards “new” and “green” development. It has successfully helped a Fortune 500 aluminum industry leader achieve digital production and refined operations, paving the way for high-quality development of the aluminum industry.
Aggregate global data to activate the “source power” of aluminum industry
Aluminum electrolysis production is a process with significant delay, multivariate coupling, and nonlinearity. Due to the high temperature and strong magnetic field environment inside the aluminum electrolytic cell, the real-time material stacking status and electrochemical reaction process inside are difficult to directly measure through sensor devices, resulting in the inability to accurately describe the production status qualitatively and quantitatively, which has become a core challenge restricting the improvement of electrolytic cell production efficiency, stability, and service life.
At the 2024 Schneider Electric Industrial Digital Ecosystem Partner Summit with the theme of “Digital Intelligence Leads Together for Win win”, Schneider Electric, a global expert in digital transformation in energy management and automation, comprehensively showcased end-to-end industrial software solutions and achievements. On site, they released two major digital solutions, the semiconductor industry factory management suite and the chemical industry safety risk intelligent control platform, and signed agreements with five leading enterprises on digital joint innovation.
Currently, empowering the construction of new industrialization with digital and intelligent technologies, accelerating the development of new quality productivity, has become an important direction for the current development of intelligent manufacturing. At the same time, cutting-edge technologies such as AI and digital twins are accelerating their integration into various application scenarios in the industrial field, providing strong impetus for enterprises to accelerate their digital and green low-carbon “dual transformation”.
At the meeting, Ding Xiaohong, Senior Vice President and Head of Industrial Automation Business in China at Schneider Electric, said, “In the current era where new quality productivity deeply empowers high-quality industrial development, opportunities and challenges coexist. Comprehensively reshaping the value chain has become a new way for enterprises to win the future. In this regard, Schneider Electric will rely on end-to-end digital solutions that fully connect industrial automation and energy management, full-service lifecycle coverage, and focus on the integration and innovation of AI and application scenarios. We will work closely with digital and sustainable ecological partners to accelerate industrial transformation and upgrading, and create future industrial influence
Ding Xiaohong, Senior Vice President and Head of Industrial Automation Business in China at Schneider Electric
Software empowers digital transformation and empowers the entire lifecycle of industrial scenarios
As an indispensable key force in the process of industrial digital transformation, the value of software has far exceeded the traditional tool category, and it is reshaping the entire future industrial ecosystem in an unstoppable way. Based on continuous innovation and profound accumulation in the field of industrial software, Schneider Electric has digital “intelligent” applications covering AVEVA industrial software solutions, ETAP power system simulation software, RIB building software, EMS energy management solutions, ProLeiT process control system, and EcoStruxure open automation platform. It can cover the information integration and management of the entire life cycle of enterprises from design, construction, operation to maintenance, helping to create enterprise level industrial data dual bases and building digital twins for users in four major industrial scenarios: engineering, assets, processes, and production.
Specifically, the engineering digital twin that integrates simulation, design, and collaboration can help enterprises build a standard driven engineering data system, improve resource utilization, and provide support for multi professional team collaboration. The asset digital twin can cover the integration of asset information from the digital delivery of projects during the construction period to the operation and maintenance period, achieving visual management of enterprise asset information. In addition, the process digital twin is based on strict mechanism models and simulation tools of the process, which can provide steady-state simulation, dynamic simulation, and online optimization to unleash the potential of process operation. Finally, the production of digital twins trains AI algorithms through industrial big data to trace, monitor, and predict process production and equipment failures. It can find the optimal operating point within the controllable domain and achieve automatic device start-up, thereby improving enterprise efficiency.
With the continuous release of application scenarios around artificial intelligence and data elements, Schneider Electric is combining its accumulated professional knowledge in the industrial field with cutting-edge AI technologies such as big language models, machine learning, and deep learning, successfully applying AI technology to industrial scenarios such as process optimization, full process carbon reduction, refined energy consumption management, air compressor energy efficiency improvement, dynamic refrigeration efficiency improvement, and predictive maintenance, promoting the development of industrial intelligence.
Release industry innovation suite, leading the industry’s “digital intelligence” upgrade
As an active enabler of industrial digital transformation, Schneider Electric has always been driven by innovation, continuously creating digital and intelligent solutions for more industries, and helping enterprises accelerate transformation and upgrading. At the meeting, Schneider Electric released two major industry digital solutions: the semiconductor industry plant management suite and the chemical industry safety risk intelligent control platform. Among them,Semiconductor Industry Factory Management Suite: By connecting and integrating various equipment and systems through the FMCS factory management system, it promotes information sharing and centralized control between equipment and systems. It not only supports mobile devices for on-site operations, improves operator efficiency, but also enables visualization of major business processes and provides reliable on-site analysis basis; Meanwhile, decision-makers can effectively improve the efficiency of planning control, periodic planning, and scheduling based on data feedback and data mining.
Intelligent control platform for safety risks in the chemical industry: Based on the AVEVA PI System operation big data management platform, the HSE safety management suite can break down data silos between different systems, establish a safety database, and provide a production safety management map according to the needs of safety production management; By combining AI with industrial vision, intelligent analysis can be further achieved to eliminate hazardous factors and non compliant operations, bringing comprehensive digital transformation to the safety production of the chemical industry.
Concentrate on the industrial digital ecosystem and achieve a win-win future
The high-quality development of industry cannot be separated from the coordinated development of industrial digital ecology. Schneider Electric combines software and hardware in the process of industrial digitization, constantly creating a safer, more efficient, and green intelligent industry ecosystem. We join hands with ecological partners committed to digital transformation and accelerating enterprise development, innovate together, and achieve win-win results. On site, Schneider Electric signed agreements with Shanghai Huayi Information Technology Co., Ltd., Anshan Huashen Control System Co., Ltd., Zhonggong Digital Technology (Suzhou) Co., Ltd., Huzhou Industrial Control Technology Research Institute, and Zhongrun Huagu (Nanjing) Technology Co., Ltd. to jointly promote digital joint innovation and continuously inject new momentum into the construction of the industrial digital ecosystem.
At the industry case sharing session of the summit, Schneider Electric also shared the latest project progress and achievements in industries such as steel, chemical, and power plants with various partners. Among them, in the steel industry pellet project, Schneider Electric’s APC advanced process control system has achieved optimized control of its main process, coal production process, and auxiliary systems, effectively improving the production stability and control uniformity of the device. The APC utilization rate is not less than 98%, and the fluctuation deviation of key control variables is reduced by more than 20%; By optimizing control and “edge locking operation”, not only has the pellet production capacity and quality been improved, but energy consumption has also been significantly reduced, helping the factory further tap into the economic benefits of the equipment.
In the digital delivery project of a newly built chemical industry factory in Henan, Schneider Electric AIA Asset Information Consultant, based on digital twin technology, can achieve visualization, intelligence, and collaboration of the entire engineering process, helping users improve engineering quality and efficiency, and reduce costs and risks. Comprehensive digital delivery services covering the entire project from construction to operation and maintenance, providing unified and standardized management for the design and procurement process, supplier drawings, construction and completion process data, while meeting users’ needs for later operation and change of the digital delivery platform.
As a digital “weapon”, Schneider Electric’s AVEVA PI System operation big data management platform has also accumulated rich “practical” experience in fields such as petrochemicals, new energy, and life sciences. For example, enterprises can rely on the AVEVA PI System to operate a big data management platform, connecting over hundreds of thousands of on-site control and information system points in their different bases, creating a group level lightweight MES deployment and control. While achieving real-time monitoring and full cycle traceability of production data, it can accelerate the efficiency of production anomaly handling and improve the response capability of the entire factory to accidents, laying a solid digital foundation for its “digital future” strategy.
As a trusted partner of the enterprise, Schneider Electric will always take digital technology innovation as the sail and industrial ecological innovation as the propeller, constantly leading more industry enterprises to sail towards the vast blue ocean of future industry together.
About Schneider Electric
Schneider Electric’s mission is to empower everyone to maximize the use of energy and resources, create impact, and promote human progress and sustainable development together. At Schneider Electric, we call it Life Is On.
Our mission is to become your trusted partner for achieving efficient and sustainable development.
As a global leader in industrial technology, we apply world leading electrification, automation, and digitization technologies to smart industries, resilient infrastructure, future oriented data centers, smart buildings, and digital homes. Based on our rich industry expertise, we provide AI enabled end-to-end full lifecycle industrial IoT solutions, covering interconnected products, automation, software, and services, and adopting cross platform industrial data bases and “digital twins” to help customers achieve profitable growth.
In the complex and ever-changing global economic environment today, the electronic manufacturing industry is facing unprecedented challenges and opportunities. To assist manufacturers in addressing these challenges, ABB and Porsche Management Consulting jointly released a white paper titled “Robot Intelligent Solutions Empowering Surface Precision Machining” at the Industry Expo held at the Shanghai National Convention and Exhibition Center on September 24, 2024, focusing on how to enhance the productivity, flexibility, and sustainability of the electronics manufacturing industry through robot automation technology. The white paper released this time not only provides profound insights for the industry, but also valuable guidance for manufacturers in their intelligent transformation.
The electronics industry, waiting for a breakthrough, is on the verge of intelligent transformation
The competition in the electronic manufacturing industry is increasingly fierce, especially in the consumer electronics field, where profit margins are constantly narrowing. According to a survey conducted by Porsche Management Consulting on 48 senior executives in the electronics industry, 96% of companies have started transitioning to smart factories to achieve productivity, reliability, flexibility, and sustainability goals, but only 8% of companies have successfully achieved these expected goals. Behind this phenomenon, it reflects the insufficient understanding of physical process automation by enterprises and the slow introduction of new technologies.
Industrial Control Network believes that in the current market environment, if enterprises do not take active actions, they may face the risk of being eliminated by the market. Due to the rapid changes in consumer demand and intensified market competition, enterprises need to accelerate digital transformation and technological upgrades to maintain market competitiveness. At the same time, intelligent transformation will no longer be a single technology introduction, but will require the integration of strategic thinking, organizational culture, and talent cultivation to comprehensively enhance the competitive advantage of enterprises.
In such an environment, the introduction of robot automation technology is particularly important. Yan Jiaxin, Deputy Manager of Global Product Portfolio for ABB Robot Systems Applications, said, “The precision requirements and rapid iteration capabilities of the electronic manufacturing industry have put higher demands on manufacturers. By adopting advanced robot automation solutions, enterprises can not only improve production efficiency, but also reduce costs and waste. For example, robot processing solutions can significantly improve output and quality, while effectively controlling production costs, thereby enhancing the profitability of enterprises. In addition, ABB hopes to use software and digital technology to empower, accelerate product development and iteration processes, create greater profit margins for customers and suppliers, and enable them to maintain industry competitiveness in rapidly changing markets
Yan Jiaxin, Deputy Manager of Global Product Portfolio for ABB Robot System Applications (right), and Dong Juntian, Partner and Industrial Product Manager at Porsche Management Consulting China (left)
It can be seen that with the continuous development of artificial intelligence and machine learning, the automation level of the electronic manufacturing industry will further improve in the future. Enterprises should not only focus on current automation technologies, but also pay attention to future technological advancements, such as intelligent robots and collaborative robots, which can better collaborate with human workers and enhance production flexibility. In addition, with the popularity of the Internet of Things (IoT), the manufacturing industry will increasingly rely on data analysis and real-time monitoring to optimize production processes, thereby achieving true intelligent manufacturing.
White paper heavyweight release, ABB robot automation solution improves efficiency and quality
The white paper provides a detailed introduction to how ABB’s robot automation solutions can help manufacturers improve productivity, especially Machining PowerPac, an offline programming tool based on RobotStudio that has the ability to automatically generate CAD path codes, making the application of robots in surface finishing more efficient.
It should be pointed out that ABB has found through past project experience and summary that manufacturers can use this technology to reduce the time required to generate robot paths from 4 hours to 3 minutes, and increase cycle time by 33%. This not only improves production efficiency, but also significantly reduces appearance damage caused by path design defects, thereby saving materials and costs. It is precisely due to the reduction of appearance damage caused by path design defects that 8000 prototype parts, equivalent to 2.37 tons of aluminum alloy, may be saved. Due to improvements in time, quality, and productivity, as well as additional savings in materials and energy, the investment in Machining PowerPac can typically be recouped within three months, with an expected return on investment of over 1200% within 18 months.
Under data validation, what you see is what you get. We can see that this successful application not only represents ABB’s leadership in the field of robotics technology, but also provides a successful case for the entire industry to learn from. At the same time, it has become an important reference for companies inside and outside the industry to invest in technology. In the future, manufacturers will increasingly rely on data-driven decision-making to evaluate the efficiency and flexibility of their production lines in real-time, in order to quickly respond to market changes and maximize production efficiency.
Furthermore, from the perspective of industrial control networks, the collaboration between ABB and Porsche Management Consulting combines the industry expertise and profound experience of both companies. Porsche’s accumulation in industry observation and in-depth analysis, combined with ABB’s leading position in the field of robot intelligent manufacturing, has made their cooperation an important force in the industry.
Dong Juntian, Partner and Head of Industrial Products at Porsche Management Consulting China, said, “In addition to the electronics manufacturing industry, we have established a deep cooperation relationship with ABB’s robot building automation team. The cooperation is not limited to these specific industries, but has also expanded to cutting-edge fields such as intelligent manufacturing, Industry 4.0, and artificial intelligence, conducting extensive and in-depth discussions and collaborations
The cross-border cooperation model will become an important trend in the future development of the industry. In the wave of intelligent manufacturing, enterprises form strong alliances through strategic alliances and technological cooperation, creating more value-added services to cope with the increasingly complex market environment. With the continuous evolution of intelligent manufacturing technology, especially in data sharing and platform construction, future cooperation will not only be the combination of products and technologies, but also the construction of ecosystems, promoting innovation and development of the entire industry.
We also hope that ABB and Porsche Management Consulting will collaborate on more diverse topics, further deepen their research and exploration in the field of intelligent manufacturing, promote greater value for electronic manufacturing enterprises in the process of intelligent transformation, and provide practical and feasible technological paths for enterprises. At the same time, electronic manufacturers should seize the opportunity of intelligent transformation, embrace new technologies, and enhance their competitiveness in the global market. In the future, with the deepening development of intelligent manufacturing, the electronic manufacturing industry will inevitably usher in new growth opportunities driven by both technological innovation and market demand.
As an economic model centered on efficient and circular utilization of resources, the concept of circular economy originated in the 1960s. At that time, American ecologist Carlson described the dangers faced by the biological world and humanity in his book “Silent Spring”. Subsequently, American economist Polding proposed to reduce the negative impact on the environment through the effective utilization and recycling of resources, and thus the circular economy began to take shape. Nowadays, global attention is increasingly focused on sustainable development and environmental protection. According to the report “The Way to Circular Economy: Towards Sustainable Development” released by Accenture, it is predicted that the overall size of the global circular economy market is expected to reach $4.5 trillion by 2030, and based on the baseline scenario estimate, the overall market will maintain high-speed growth at a compound annual growth rate of 10.7%. Circular economy has become an ideal economic model for achieving sustainable development.
China is accelerating its comprehensive green transformation, and the circular economy is also entering a new period of rapid development in the domestic market. In March of this year, the State Council issued the “Action Plan for Promoting Large scale Equipment Renewal and Consumer Goods Trade in”, which included “recycling and reuse” as one of the four major implementation actions. Subsequently, specific plans were intensively implemented in various fields such as industry, transportation, and energy. On August 11th, the State Council issued the “Opinions on Accelerating the Comprehensive Green Transformation of Economic and Social Development”, proposing to “vigorously develop the circular economy, deepen the promotion of circular economy to help reduce carbon emissions, promote resource recycling production models; vigorously develop the resource recycling industry, and expand the scale of substitution for primary resources
Under the promotion of policies, it is expected that by 2030, the scale of the energy-saving and environmental protection industry will reach about 15 trillion yuan, and by 2035, the green, low-carbon, and circular development economic system will be basically established. The rise of the trillion dollar market heralds a new round of accelerated development of the circular economy.
Seizing the opportunities of circular economy requires enterprises to undergo systematic changes, which require executable paths and joint efforts from internal and external stakeholders. The systematic transformation of the circular economy is not only about shifting from the traditional linear model of “acquisition, manufacturing, and disposal” to a circular model that promotes resource efficiency, reduces waste, and creates value, but also involves comprehensive transformation at all levels of consumption and production. This includes: using Design&Innovation as the cornerstone, achieving a closed-loop circular economy through Use better, Use longer, and Use again.
Centered around the innovative circular design concept, enterprises should choose green materials to ensure product “optimal use”, select low-carbon suppliers’ green materials, and use digital technology to improve product traceability, ensuring high-quality production of products. At the same time, timely maintenance, renovation, and modification should be carried out according to the usage of the product to extend its service life and achieve “long-lasting use” of the product. Finally, after the product reaches its service life, it is repackaged and refurbished, and the raw materials are recycled to implement “reuse” and avoid further resource consumption.
The ‘Green Path’ of Circular Economy Practitioners
As a practitioner of sustainable development, Schneider Electric incorporated sustainability into its core strategy as early as 2002 and integrated it into all aspects of business operations. The core of circular transformation lies in the “design and innovation” stage, which affects product development and innovation. Schneider Electric adopts a full lifecycle thinking approach to develop and design new products, taking into account materials, packaging, energy use, and recycling processes to ensure that products are easy to maintain and recycle. We also provide designers and engineers with tools and training such as carbon emission calculators, striving to improve the environmental impact of our products through innovative ecological design.
The key to the “optimal use” stage is to procure sustainable raw materials and minimize waste as much as possible. For example, Schneider Electric has increased the use of green materials in its products to 32%, and 70% of its products replace disposable plastic packaging with recyclable cardboard, achieving multiple uses and recycling. In addition, in terms of promoting industry development, as of the second quarter of 2024, Schneider Electric has helped 1000 major suppliers worldwide reduce carbon emissions by an average of 33% at the operational level through the supplier’s “Zero Carbon Plan”.
In addition to using recycled materials and renewable energy, the operation of green and smart factories also promotes a circular economy by creating new efficiencies and flexibility. Schneider Electric has 30 factories and logistics centers in China, including 18 smart factories and smart logistics centers. Meanwhile, 15 factories have been recognized as green factories by the Ministry of Industry and Information Technology.
Thanks to its outstanding achievements in the field of “circular economy”, Schneider Electric was awarded the title of “Circular Lighthouse” in the field of built environment by the World Economic Forum and McKinsey&Company during the 2024 Annual Meeting of the World Economic Forum, providing an excellent example for enterprises from all walks of life to collaborate on green transformation of the value chain.
As an enabler of sustainable development, Schneider Electric deeply understands that circular economy is a systematic engineering, and only through industrial cooperation and mutual empowerment can sustainable innovation and systematic transformation be achieved. To this end, Schneider Electric has launched services including “EcoConsult Consulting Services,” “EcoCare Operations Services,” and “EcoFit ™ The newly upgraded new quality service system, including “adaptation and transformation services”, helps more enterprises integrate into the circular economy.
For example, in the “long-term use” stage, users can extend the product’s lifespan through repair, digital maintenance, and longevity services. According to statistics, Schneider Electric’s “EcoCare Operations and Maintenance Services” and “EcoFit ™ Adaptation and transformation services can help extend the service life of customer assets by up to 25%, thereby reducing the carbon footprint of equipment. Therefore, in 2023, Schneider Electric established EcoFit in Xiamen ™ The Adaptation and Transformation Capability Demonstration Center provides end-to-end capabilities from structural design, component design, factory manufacturing to on-site installation to help customers effectively extend product lifecycle and reduce overall costs.
The ‘reuse’ stage covers the recycling of products, components, and materials. At the just concluded 2024 China International Fair for Trade in Services, Schneider Electric officially released the Circular Offer variable frequency cycle machine. When the frequency converter used by customers experiences aging and malfunctions, and there is a need for emergency spare parts, replacement repairs, low-cost upgrades, and other modifications, product information can be provided to Schneider Electric’s service partners to order the same Circular Offer frequency converter at a lower price. Service partners will ship within 24 hours of receiving the order, while Schneider Electric will repair and refurbish the frequency converters returned by customers, thereby achieving the recycling of old frequency converters. The Circular Offer variable frequency cycle machine manufactured by Schneider Electric is not only fully compatible with the new machine in terms of functionality, but also maintains consistent performance and quality assurance with the original factory standards. Customers can enjoy the same quality as new machines at a lower cost, fully reflecting the concept of circular economy.
Schneider Electric Circular Offer Variable Frequency Cycle Machine
As a practitioner and enabler of sustainable development, Schneider Electric’s commitment to the circular economy began over 20 years ago and continues to this day. Schneider Electric is committed to transforming the concept of circular economy from theory to the core of its business, contributing to the construction of a new pattern of green, circular, and low-carbon economic development. Looking ahead to the future, Schneider Electric will continue to use the “new quality service system” as a starting point, relying on its practical experience in sustainable development, as well as its industry ecosystem and comprehensive service capabilities covering multiple fields, to empower major industries to take advantage of the development trend of circular economy, move towards greenness, and remain fresh over time.
The Yaskawa exhibition site can be described as crowded and lively. Industry experts, business representatives, and audiences from around the world gathered together to witness Yaskawa’s latest achievements and innovative technologies in the industrial field. The atmosphere on site was lively, with constant communication and admiration, fully demonstrating everyone’s high attention and expectations for Yaskawa.
Exciting Moments at the Yaskawa Exhibition Site
I ³ – Mechatronics is committed to producing new quality products
Empowering future development
At this industrial expo, Yaskawa brought a series of eye-catching exhibits. From high-precision industrial robots to intelligent control systems, every exhibit embodies Yaskawa’s wisdom and innovative spirit. These exhibits not only showcase Yaskawa’s strong capabilities in technology research and development, but also bring new ideas and solutions for the development of the industrial sector.
Robot Exhibition Area
Collaborative robot welding workstation
Related products: Yaskawa Robot HC10DTP, Funex TPS400i Welding Power Supply System
Application industries: automotive parts, arc additive manufacturing
Application scenarios: Suitable for various application scenarios of automotive parts such as sub frames, various steel structures, pipelines, flanges, pressure vessels, arc additive manufacturing, etc.
Product advantages: Collaborative robots, with their flexibility, efficiency, and safety features, can meet customized product needs, have higher flexibility and efficiency, and cope with production tasks of multiple varieties and small batches.
Performance parameters: Load of 10kg, Smart PP teaching pendant
Exhibition introduction: The human-machine collaborative robot welding unit consists of a Funex welding power supply system, a welding platform, and an Yaskawa HC10DTP collaborative robot.
Combining the technological advantages of both parties, Yaskawa Funex provides customers with a customizable welding solution. The Yaskawa offline programming software MotoSim EG-VRC, combined with the Funence welding process package, not only achieves efficient welding operations, but also further enhances the flexibility and quality of welding by quickly calling standard parameter libraries and optional CMT cold metal transition processes. In addition, this human-machine collaborative welding workstation has better spatial accessibility compared to traditional robot welding. Suitable for various application scenarios of automotive parts such as sub frames, various steel structures, pipelines, flanges, pressure vessels, arc additive manufacturing, etc., it can help enterprises significantly improve operational efficiency and expand production capacity on the production line.
Robot machining center and friction stir welding unit
Product involved: GP250; SGMRV-13ANA-YR11 (external axis); MS-RT14-013 (Tuolaiyi spindle), V1000 (inside welding machine cabinet)
Application industries: New energy, lithium batteries, and others
Application scenarios: machining+drilling+cutting+polishing, new energy and lithium batteries, automotive industry, heavy industry and other industries
Product advantages: High rigidity, high-precision robots can achieve drilling, cutting, polishing, friction stir welding in different scenarios, assisting in flexible production.
Exhibition machine introduction: With the configuration of GP250+Tuolaiyi FSW, it is easy to meet the welding needs of large products. The characteristics of large movable range and collaborative processing improve the layout space efficiency and shorten the processing time. And the use of quick change tools meets the processing requirements before and after the production line.
Human machine collaborative textile machine
Product involved: Human robot collaborative robot HC10DTP
Application industry: Textile industry
Application scenario: Collaborative textile operations between humans and robots
Product advantage: Collaborative operation between humans and robots, safe and reliable
Performance parameters: Load of 10kg, Smart PP teaching pendant
Exhibition introduction: Robots and humans collaborate to weave a new future of traditional industry and modern technology.
Swipe left and right to view more
Sports Control Exhibition Area
Energy Storage Cell Stacking Demonstration Machine
Related products: Motion controller MP3000, linear motor SGLVW2, servo product ∑ – X series
Application Industry: Energy Storage Technology (Lithium Battery)
Application scenario: Lithium battery cell stack
Product advantages: The MP3000 series motion controller provides multi axis highly coordinated and synchronized motion control support; The ∑ – X series servo products provide stable and high-quality driving force; The battery laminating machine has significantly improved in accuracy, efficiency, and reliability; Yaskawa provides mature battery manufacturing solutions for the automotive battery market.
Exhibition machine introduction: This equipment includes multiple key components, such as cell winding, positive electrode sheet handling, negative electrode sheet handling, diaphragm tension control, etc. The equipment adopts an advanced tension control system to ensure that the diaphragm tension remains constant throughout the entire winding and laminating process. This can not
only improve the production efficiency of batteries, but also significantly enhance the quality and consistency of batteries.
In addition, each action of the device is driven by high-precision servo motors and controlled and coordinated in real-time through the MECHATROLINK-III/4 communication system. This efficient communication and control system enables devices to maintain high accuracy and reliability even at high speeds.
Energy storage cell winding demonstration machine
Related products: Motion controller MP3000, servo product ∑ – X series
Application Industry: Energy Storage Technology (Lithium Battery)
Application scenario: lithium battery cell winding
Product advantage: The MP3000 series motion controller provides multi axis highly coordinated and synchronized motion control support. The ∑ – X series servo products provide stable and high-quality driving force. Facing the consumer battery market, Yaskawa provides mature battery cell manufacturing solutions.
Exhibition introduction: YASKAWA Cockpit integrates lithium battery production lines, visualizes and analyzes equipment production data and core data for reuse. Based on the Yaskawa i ³ – Mechatronics concept, combined with the comprehensive application of Yaskawa products, the ultimate goal is to achieve closed-loop optimization of the production performance of wound batteries, and achieve dual improvement of winding quality and efficiency.
Thrust Assist Function Demonstration Machine
Related products: Servo products ∑ – X series
Application industry: General industry
Application scenarios: Semiconductor, LCD, 3C
Product advantages: gantry position compensation, improving the synchronization of gantry structure; Multi action thrust assist to solve the problem of insufficient thrust in narrow and long spaces with small straight lines; Exhibition introduction: This equipment adopts advanced torque and thrust assistance functions, which can effectively solve the problems of insufficient mechanical installation space and insufficient output force on one side of the gantry structure.
By using two different power MECHATROLINK-III communication ∑ – XS servo drives, the gantry structure is jointly driven.
Fixed point output function demonstration machine (fixed focus flying shot distance measurement)
Related products: Servo products ∑ – X series
Application industry: General industry
Application scenarios: Application scenarios that require fast response, precise control, and high-speed detection, such as 3D line laser sensors, semiconductor vision inspection, etc
Product advantages: Fixed point output function, utilizing servo hardware characteristics to output signals at designated points, striving for precision in position, reducing the errors and compensation values that the control system needs to process.
Exhibition machine introduction: The servo with fixed-point output function can be used to directly detect the passing position from the encoder position through the fixed-point output system, and output the camera trigger signal, effectively shortening the signal processing cycle with minimal delay. Servo with fixed-point output function is often applied in application scenarios that require fast response, precise control, and high-speed detection, such as 3D line laser sensors, semiconductor vision inspection, etc.
Tension control function demonstration machine
Related products: Servo products ∑ – X series
Application industry: General industry
Application scenarios: Printing industry, packaging, lithium battery winding
Product advantage: Tension control function ensures tension stability during material feeding process. Reduce subsequent production problems caused by unstable material tension and improve production efficiency.
Introduction to the exhibition machine: The servo unit with tension control function can directly read the tension sensor signal for tension control, maintaining a constant tension, and can be achieved through simple setting and adjustment. The tension control processing time is in microseconds.
In addition, in the face of rapid load changes, it can be quickly adjusted to achieve smooth tension control and improve product quality.
Collision perception function demonstration machine
Related products: Servo products ∑ – X series
Application industry: General industry
Application scenarios: Solid crystal machines, sorting machines, welding machines, robotic arms, laser processing, etc
Product advantages: Collision sensing function, effectively improving equipment safety, reducing material damage during production process, and increasing yield rate.
Exhibition machine introduction: Collision sensing servo is generally used in semiconductor industry’s solid crystal machines, sorting machines, welding machines, robotic arms, laser processing, etc. During equipment operation, sometimes due to abnormal loads, the motor may experience sudden torque changes. The collision sensing function servo can monitor the motor torque value in real time, detect mechanical abnormalities, and obtain workpiece information.
Maintenance work is only carried out when an alarm is triggered. The use of collision sensing servo function can reduce equipment failures caused by previous component damage, reduce the number of repair operations, and lower maintenance costs.
Visitors from all directions gather together
Witness the glorious moment of Yaskawa