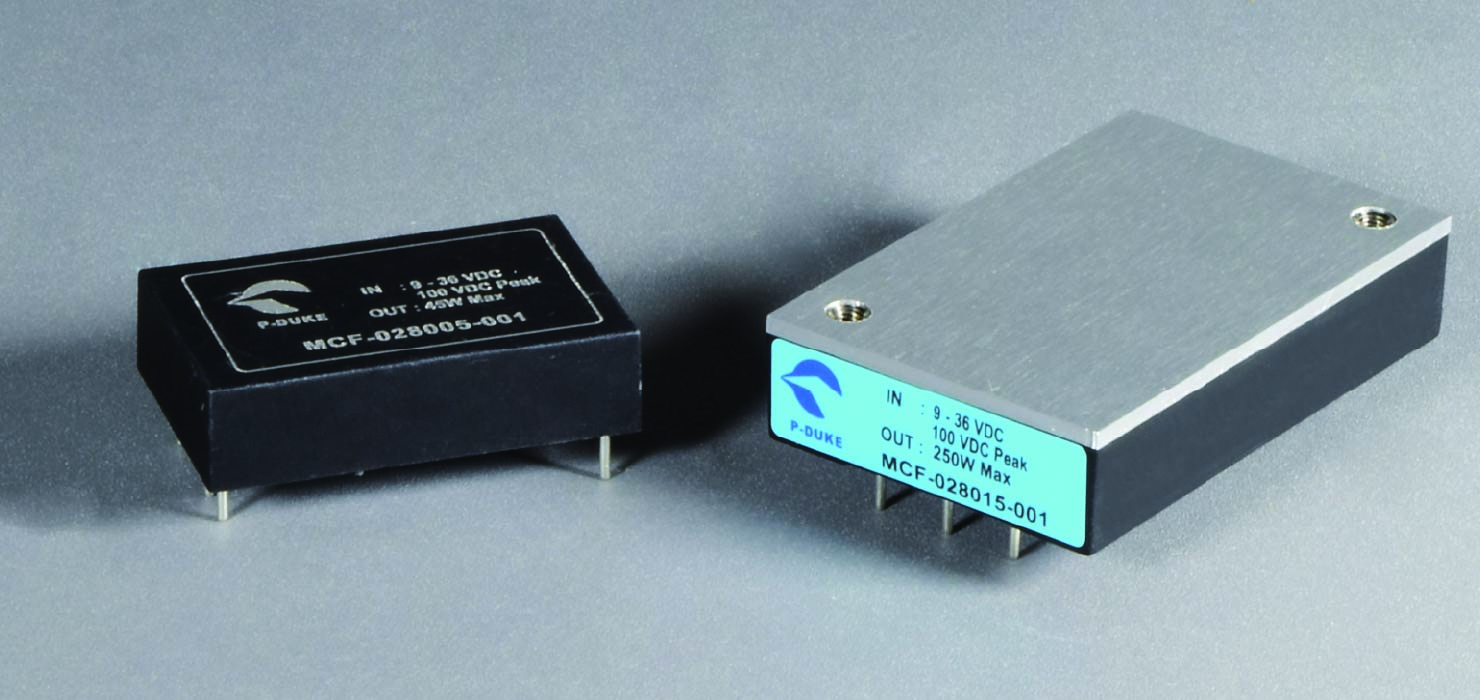
The switching action of DC-DC converters may cause adverse common mode and differential mode noise, creating unacceptable interference at many points in the spectrum. Front end (or power line) filters are designed to be used before DC-DC converters to mitigate electromagnetic interference (EMI). These customizable or readily available front-end filters can be designed to comply with electromagnetic compatibility (EMC) regulatory standards, such as FCC, ETSI, CISPR, MIL-SPEC, with suppliers’ switch mode power supplies (SMPS) or DC-DC converters.
These ready-made front-end filters are custom designed based on the electromagnetic characteristics of power conversion equipment. However, other electrical (such as voltage spikes, ripples), mechanical (such as vibration, shock), and environmental (such as high altitude) design limitations must also be considered to meet the needs of military equipment. This article discusses the design considerations for front-end filters and the testing requirements for DC power modules in military equipment.
What is a front-end filter?
The design of this input filter is crucial for meeting electromagnetic compatibility (EMC) standards and objectives. Front end or input filters are used for various purposes:
Suppress noise and spikes that may enter the first stage of the power supply,
Reduce the emission noise of the fundamental frequency (i.e. switching frequency) and its harmonics
The design of this input filter is crucial for meeting electromagnetic compatibility (EMC) standards and objectives. Front end or input filters are used for various purposes:
Suppress noise and spikes that may enter the first stage of the power supply,
Reduce the emission noise of the fundamental frequency (i.e. switching frequency) and its harmonics
The use of switch mode power supplies in electronic devices is becoming increasingly common, with rich spectral content that may be transmitted to other parts of the circuit through physical contact and interfere with nearby sensitive circuits. As the switching speed increases, noise becomes an increasingly significant issue, especially when fast switching transistors cause interruption of current flow (resulting in voltage spikes and high-frequency noise). These current interruptions can be found at the input of the buck converter, the output of the boost converter, as well as the input and output of the flyback and buck boost converters.
Noise sources of various voltage regulators
The input terminal of the DC/DC buck converter has fast switching devices that quickly turn on and off, resulting in sharp rising and falling edges (high di/dt) of intermittent current on the capacitor. This will result in the fundamental frequency and several harmonics (usually low order harmonics) not meeting the standard. A boost converter operating in continuous conduction mode (CCM) will experience EMI at its output due to the need for a fast reverse recovery diode. Although this greatly reduces power loss, the current change (di/dt) is more aggressive, increasing EMI. In discontinuous conduction mode (DCM), the main current ripple is larger. Ripple will create a changing signal, which will be conducted to other parts of the system through a common contact conductor.
The input terminal of the DC/DC buck converter has fast switching devices that quickly turn on and off, resulting in sharp rising and falling edges (high di/dt) of intermittent current on the capacitor. This will result in the fundamental frequency and several harmonics (usually low order harmonics) not meeting the standard. A boost converter operating in continuous conduction mode (CCM) will experience EMI at its output due to the need for a fast reverse recovery diode. Although this greatly reduces power loss, the current change (di/dt) is more aggressive, increasing EMI. In discontinuous conduction mode (DCM), the main current ripple is larger. Ripple will create a changing signal, which will be conducted to other parts of the system through a common contact conductor.
EMI: Emission of radiation and conduction
Typically, conducted emissions are associated with frequencies below 30MHz, while radiated emissions typically fall within the frequency range above 30MHz (typically 50 to 300MHz). However, there is still overlap between the emission of conduction and radiation. In switch mode power supplies, voltage spikes (high dV/dt) are usually the source of radiated noise. As mentioned earlier, conducted EMI typically originates from intermittent currents (high di/dt) and can be decomposed into common mode (CM) and differential mode (DM) noise.
Typically, conducted emissions are associated with frequencies below 30MHz, while radiated emissions typically fall within the frequency range above 30MHz (typically 50 to 300MHz). However, there is still overlap between the emission of conduction and radiation. In switch mode power supplies, voltage spikes (high dV/dt) are usually the source of radiated noise. As mentioned earlier, conducted EMI typically originates from intermittent currents (high di/dt) and can be decomposed into common mode (CM) and differential mode (DM) noise.
Differential and common mode noise
The DM current is usually dominated by di/dt and will flow between the power line and the circuit; DM noise dominates lower frequencies. It is usually difficult to change the behavior of di/dt without fundamentally altering the circuit. By using passive low-pass EMI filters (such as R-C dampers, L-C, Pi sections, T sections, etc.) to suppress oscillations caused by intermittent currents, di/dt can be reduced.
The DM current is usually dominated by di/dt and will flow between the power line and the circuit; DM noise dominates lower frequencies. It is usually difficult to change the behavior of di/dt without fundamentally altering the circuit. By using passive low-pass EMI filters (such as R-C dampers, L-C, Pi sections, T sections, etc.) to suppress oscillations caused by intermittent currents, di/dt can be reduced.
The CM current is usually a function of dV/dt and will flow between each power line and ground. When CM current is coupled into a long conductor or cable, the cable can act as an antenna, making CM noise more prominent at high frequencies. Based on the length of the cable, the distance between the conductors, and the reference ground plane, the loop area of an unexpected circuit may be very large. Effective layout design can greatly suppress CM, such as moving conductors closer to the reference ground plane, carefully deploying safety capacitors, shielding connected cable bundles, or placing CM inductor coils in the CM current path. The CM inductor coil also provides a high impedance series path, allowing the CM current to form an EMI ground shunt path through the Y capacitor and flow out of the converter.
Both DM and CM will contribute to EMI, and it is often necessary to quantify the noise components of DM and CM before designing EMI filters to comply with industry EMC standards. Input EMI is typically quantified using a Line Impedance Stabilization Network (LISN) at the input of the Device Under Test (DUT) and a spectrum analyzer.
Design considerations for front-end filters
Design considerations for front-end filters
Usually, passive EMI filtering is the most common method for noise suppression; However, this may prove difficult when the filter terminates with different load impedances and different noise sources of the SMPS. These filters are typically various arrangements of resistors, capacitors, and inductors. The fundamental components and the first few harmonics have the largest magnitude and will make the greatest contribution to the overall noise, while the amplitude of higher-order harmonics gradually decreases as the frequency increases. The ability of filters to suppress these noise components also increases with increasing frequency, therefore, reducing noise at the fundamental frequency and low order harmonics is a prominent design challenge.
Usually, large passive filters can alleviate low-frequency emissions; However, due to its parasitic properties such as the equivalent series resistance and inductance of capacitors, as well as the parallel capacitance of inductors, high-frequency emission may require additional design considerations. Other EMI filtering techniques typically involve active components: one technique is to use spread spectrum or jitter to modulate the switching frequency of the power supply, in order to reduce the peaks of fundamental and low order harmonics found in the frequency domain. Ultimately, the technology adopted depends on the unique noise characteristics of the SMPS, as well as design costs, size, and regulatory limitations.
In addition to complying with EMC regulatory standards, EMI filters can also include the ability to suppress high current transients reflected from the load to the input power supply of the SMPS. The predicted transient characteristics of each SMPS will vary, so custom design is usually required to fully suppress spikes. This is undoubtedly an additional design consideration for MIL-SPEC power electronic devices. Military equipment will have a range of electrical, mechanical, and environmental design considerations that will require manufacturers to carefully design power electronic devices from the basics – they must meet material selection and electrical, mechanical, and harsh environmental performance requirements.
Common military standards for power supply
MIL-STD-461 sets conduction and radiation emission limits for electrical equipment to guide proper measurement of EMI. If the SMPS exceeds these limits – which it often does – it will require an EMI filter to ‘bring it back to specification’. However, choosing any ready-made EMI filter does not necessarily result in the power supply suddenly meeting the standard requirements; The device may be so noisy that attaching any EMI filter to the input will still cause the component to fail. The various requirements and descriptions of MIL-STD-461 can be found in Table 1. Electronic devices that comply with MIL-STD-461 typically list detailed information that meets specific CE, CS, and RE requirements.
MIL-STD-461 sets conduction and radiation emission limits for electrical equipment to guide proper measurement of EMI. If the SMPS exceeds these limits – which it often does – it will require an EMI filter to ‘bring it back to specification’. However, choosing any ready-made EMI filter does not necessarily result in the power supply suddenly meeting the standard requirements; The device may be so noisy that attaching any EMI filter to the input will still cause the component to fail. The various requirements and descriptions of MIL-STD-461 can be found in Table 1. Electronic devices that comply with MIL-STD-461 typically list detailed information that meets specific CE, CS, and RE requirements.
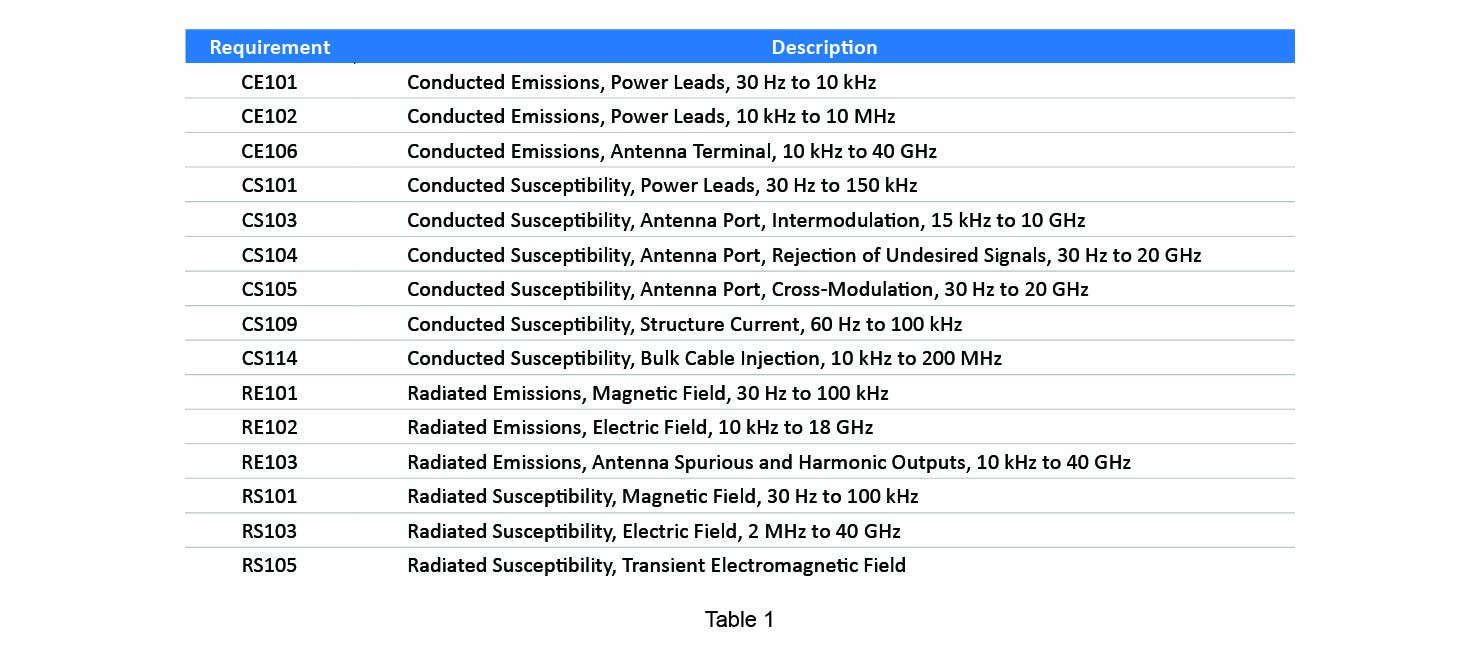
EMI is not the only consideration for the correctness, reliability, and safety of electronic devices. The power supply must also be able to operate under various voltage conditions, including reverse polarity, voltage spikes, and voltage surges. The MIL-STD-1275E standard provides the testing conditions to be applied to the input of a 28V electrical power system, as well as the expected performance parameters of the equipment. These systems are expected to be used for military ground vehicles, civilian off-road vehicles, as well as military and civilian heavy equipment.
Other military standards, such as MIL-STD 704F for aircraft electrical characteristics and DO-160G for onboard equipment, will specify environmental conditions and testing procedures to fully simulate various voltage conditions. The MIL-STD-810 standard includes testing conditions and requirements for equipment that will undergo mechanical shock, vibration, and high altitude. This may also be a necessary consideration to ensure long lifespan and reliability of the supply in harsh environments. The power sources operating in military vehicles and aerial systems may need to meet various aspects of MIL-STD-1275E/MIL-STD 704F, MIL-STD-461, and MIL-STD-810 to be considered suitable for use. P-Duke offers a range of MCF military grade front-end filters that can be matched with selected DC/DC converters to meet all of these specification requirements.
P-DUKE MCF series
The MCF series provides EMI filtering and transient protection to meet the conducted emission, conducted sensing, and radiated emission requirements of MIL-STD-461G standard, surge/spike requirements of numerous military standards, and height/shock/vibration requirements of MIL-STD-810 (Table 2).
The MCF series provides EMI filtering and transient protection to meet the conducted emission, conducted sensing, and radiated emission requirements of MIL-STD-461G standard, surge/spike requirements of numerous military standards, and height/shock/vibration requirements of MIL-STD-810 (Table 2).
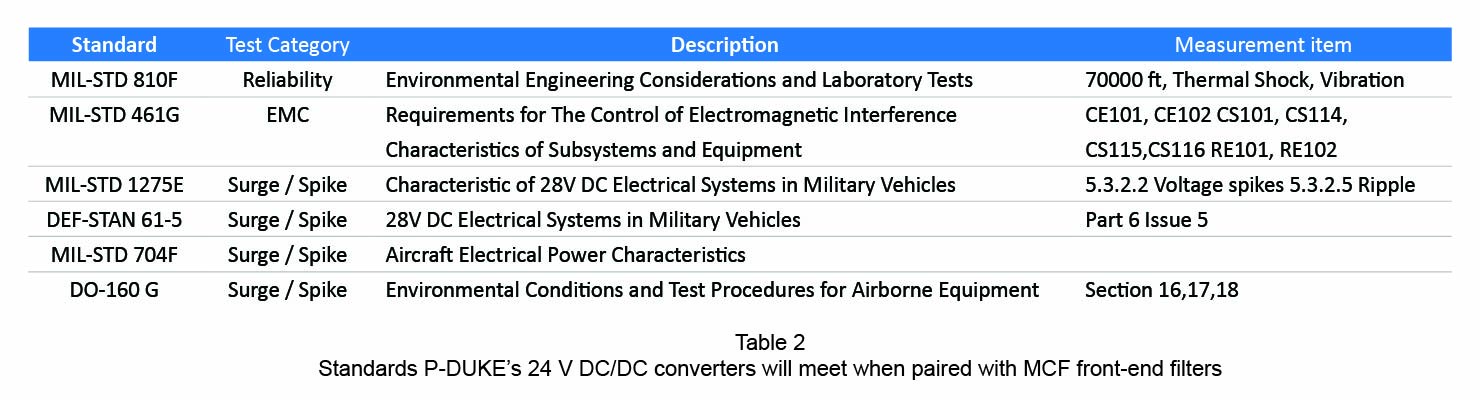
This series has active input overvoltage protection function, which can limit the maximum duration of 50ms overvoltage to below 40V, absorb peak voltage of+/-250V, and is equipped with internal protection circuit (Figure 1).
As shown in Figure 2, this series includes other active protection functions, such as remote on/off control, overload protection, output short circuit protection, reverse polarity protection, startup current limitation, etc.
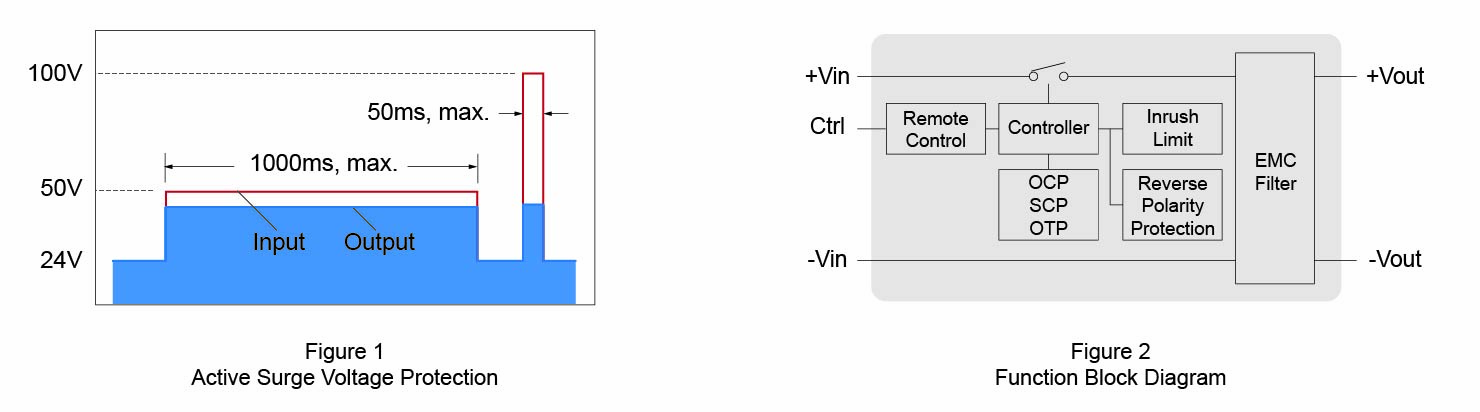
In Figure 3, it can be seen that the EMI performance has been significantly improved. The EMI performance of a 200W HAE200 DC/DC converter was tested before and after applying the MCF filter. This greatly reduces the cost and design workload of customizing EMI filters and peripheral circuits. The MCF front-end filter has a rated power of up to 250W and can be used in a wide range of military equipment.
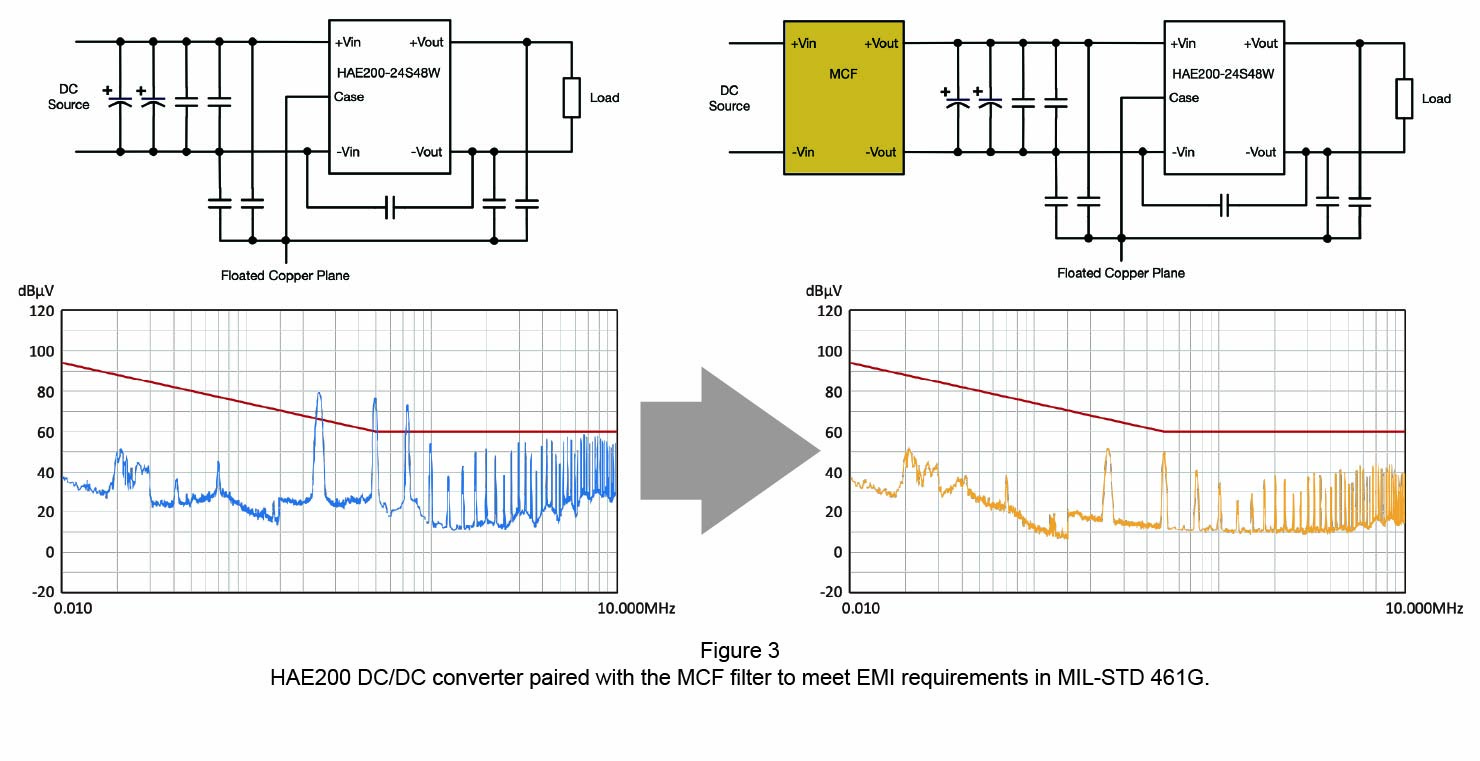
MCF filters can be simplified and integrated into military systems
EMI filters cannot be simply selected arbitrarily to ensure that the power supply meets standards. The process of designing these filters can be very complex and have high Non Repetitive Engineering Costs (NRE). This is particularly true in military equipment, where onboard subsystems in military vehicles and aircraft are powered by 24V batteries or 28V generators, which have strict requirements for multiple aspects, and COTS equipment and customized solutions may not be feasible. P-DUKE provides DC-DC converters ranging from 15W to 250W, paired with relevant MCF front-end filters, to meet military requirements for EMC and surge suppression.
EMI filters cannot be simply selected arbitrarily to ensure that the power supply meets standards. The process of designing these filters can be very complex and have high Non Repetitive Engineering Costs (NRE). This is particularly true in military equipment, where onboard subsystems in military vehicles and aircraft are powered by 24V batteries or 28V generators, which have strict requirements for multiple aspects, and COTS equipment and customized solutions may not be feasible. P-DUKE provides DC-DC converters ranging from 15W to 250W, paired with relevant MCF front-end filters, to meet military requirements for EMC and surge suppression.
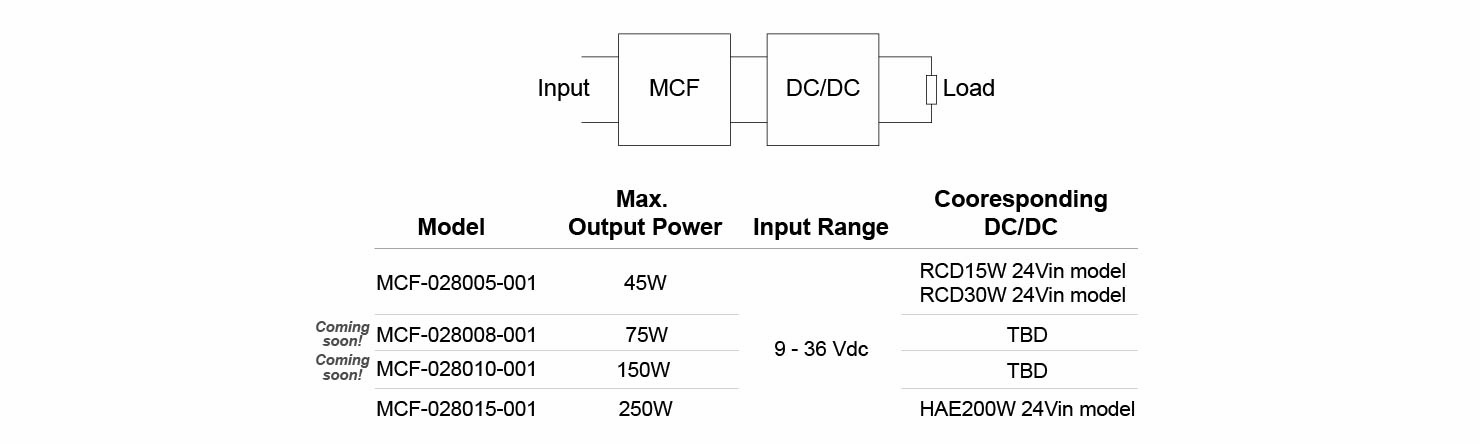
Leave a comment
Your email address will not be published. Required fields are marked *